Industrial Tank Cleaning Services
SERVICE
TANK CLEANING
For over 20 years NICO I.S. has been working in the tank cleaning sector using an innovative tank cleaning process called “NicoTank” for cleaning crude oil storage tanks through an automatic process suitable for cleaning all types of tanks (both fixed roof and floating roof tanks) and recover hydrocarbons. The tank cleaning process is based on the principle of mechanically liquefied hydrocarbon sediments by injecting crude oil or fuidifying agents into the closed tank through a jet washer (that is mounted in the transport pipes of the roof tank and on the bottom through the manholes) and using energy and heat during the process. In the first stage of the Nico Tank process, the sludge is dissolved with crude oil or other solvents and once the hydrocarbons are separated, they are ready for the refinery.
NicoTank is a closed circuit tank cleaning system, which is considered practical and safe and helps reduce to a minimum the entry of personnel within confined spaces. Once the work site is set up, nozzles are placed on the manholes of the tank. When and if the tank level is above the level of the manhole, the nozzles are installed with the use of special ‘HOT TAP MACHINE’. This system allows the installation of the nozzles on the manholes, while cold cutting them.
Next, gas, oil or other middle distillate can be used to dissolve and recover further hydrocarbons from the residues and from the sediment layer on the bottom of the tank. The sludge that dredges out from the tank is now ready to be treated in a “Centralized Sludge Treatment Facility”. The technology used by NICO I.S. includes the circulation and fluidification of the product and the use of a three-phase and two-phase centrifugation station that allows the recovery of hydrocarbons and reduces to a minimum the waste to be disposed of. Now the solid waste may be treated using a drying system called NICODRYER, which operates in a slightly depressurized closed circuit, with water and oil condensation.
In order to assess the recovery of valuable substances the composition of the sludge needs to be evaluated. Typical sludge is made up of 80% – 90% heavy Hydrocarbons and paraffin, 5-20% water and 3-5% non organic materials.
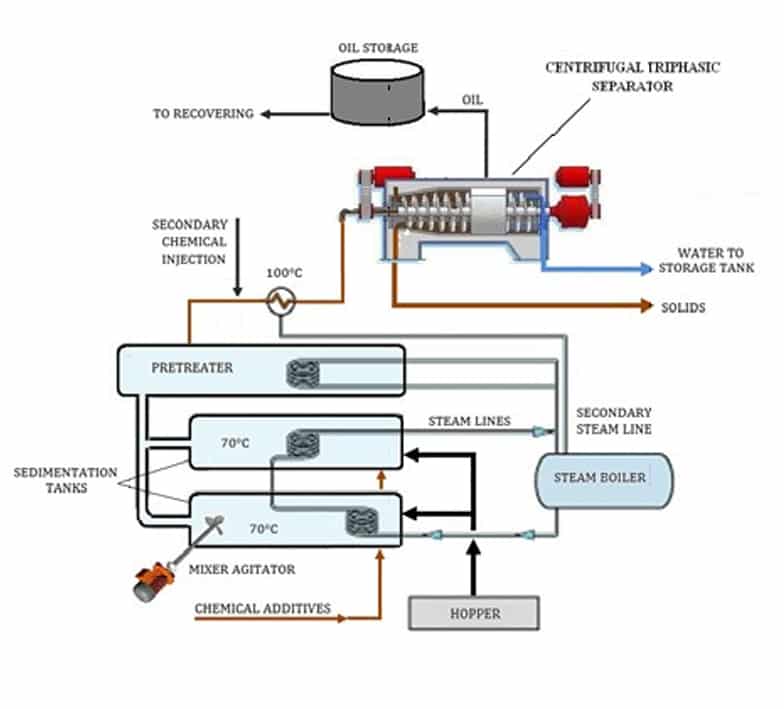
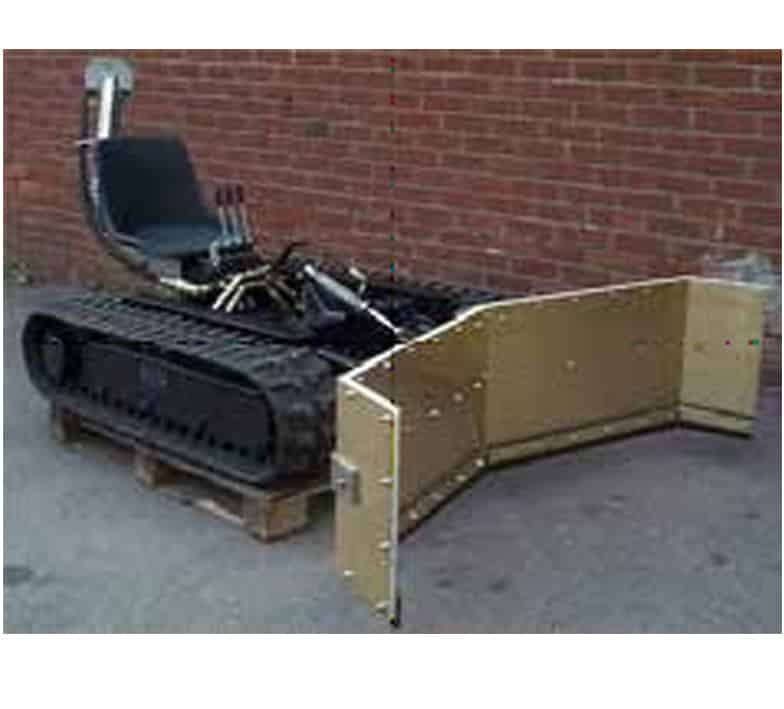
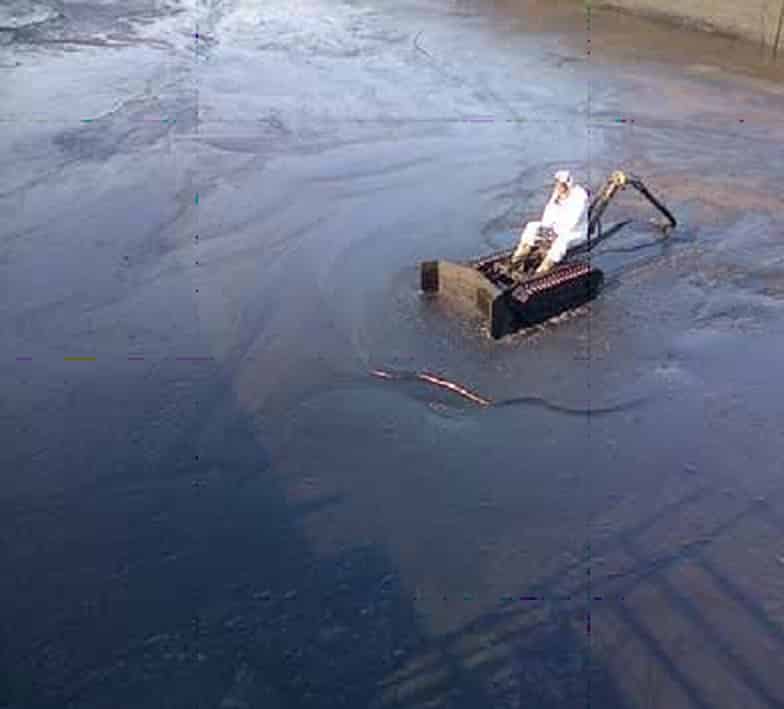
The configuration of the Centrifugation Plant with a “pre-teater”, decanter and vertical disc centrifuge allows the reach of high quality separated oil, water with low content of oil and solids and a minimum quantity of waste for the landfill.
When the product level is below the level of the manhole and it isn’t possible to continue with the circulation, the entire circuit is dismantled and the manholes are opened. In the case when some residues of sludge are still present, it is possible to use the NES-MOVER system, (later described in more detail), which allows the final cleaning phase to be carried out and requires only 1 technician to enter within the tank.
At the end of the process, a final washing of the walls, roof and tank floor is performed, in order to obtain a Gas Free environment within the equipment.
The NES-MOVER system comprises of several individual components:
- The MOVER;
- The lobe pump;
- Umbilical storage reels;
- Diesel driven hydraulic power pack.
The NES-MOVER system is a purpose built tank cleaning tool for large diameter above ground storage tanks; The NES-MOVER system is proven to be the fastest and most efficient way to carry out desludging operations; typical desludging rates of up to 200 m³ per day can be achieved with an experienced operator. The system is controlled by an operator on board car. Such system can be used alone or together to a previous cleaning phase through a closed circuit circulation system.
The system is certified in accordance with the latest ATEX directives.
Thanks to a stern and continuous collaboration with the University of Catania – Department of Industrial Engineering – new trials related the activity of Tank cleaning have recently been developed. Taking advantage of the use of last generation technologies and equipment, the new NicoTank process has allowed us to reach the following objectives:
- Reduction of the time needed for the installation of the equipment.
- Installation of the equipment with non-invasive and applicable methodologies also for tanks which are not in optimal conditions.
- Reduction of the number of specialized technicians within the tank for the final reclamation operations.
- Reduction of the total reclamation time.
- Recovery of a high percentage (around 90%) of hydrocarbons present within the tank.
- Reduction of the total quantity of waste to be taken to the waste pit.
- Reduction of the total costs related to the operations of reclamation and waste disposal.
SERVICE
BLABO® TANK CLEANING
BLABO® is an automated no man entry system and cutting-edge technology developed and introduced to the market by ORECO®.
BLABO® is a mobile, modular tank cleaning and oil recovery system for large storage tanks with floating or fixed roofs, handling heavy fuel oil, crude oil and the like.
- The BLABO® system sets new standards for safe, environmentally friendly and cost-efficient tank cleaning.
- The automated BLABO® method has been used to clean hundreds of oil storage tanks with fixed and floating roofs.
- The patented BLABO® system operates safely in potentially hazardous environments.
BLABO® is a non-man entry system. Operators do not work inside the tank and are not exposed to hazardous situations during cleaning. - Operators are thoroughly trained by ORECO® to operate the system and perform the strictest safety procedures.
- The complete operation is continuously monitored by a buit-in process control and automatic shutdown features.

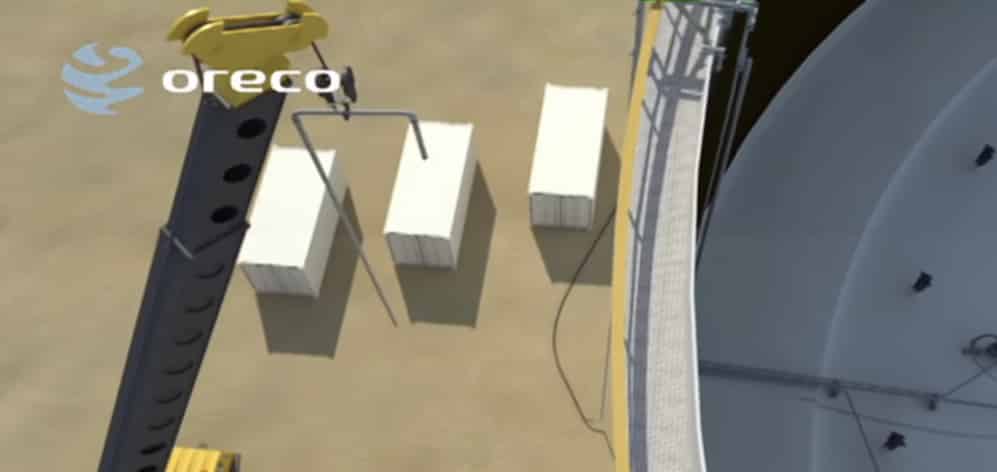
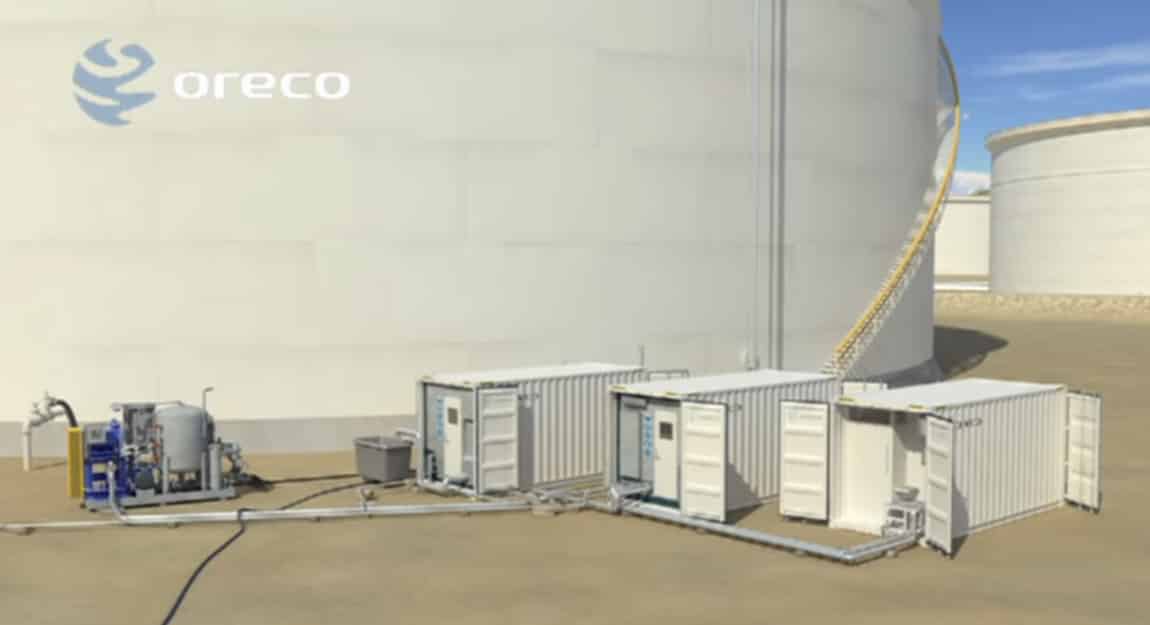
NOZZLE INSTALLATION IN THE ROOF
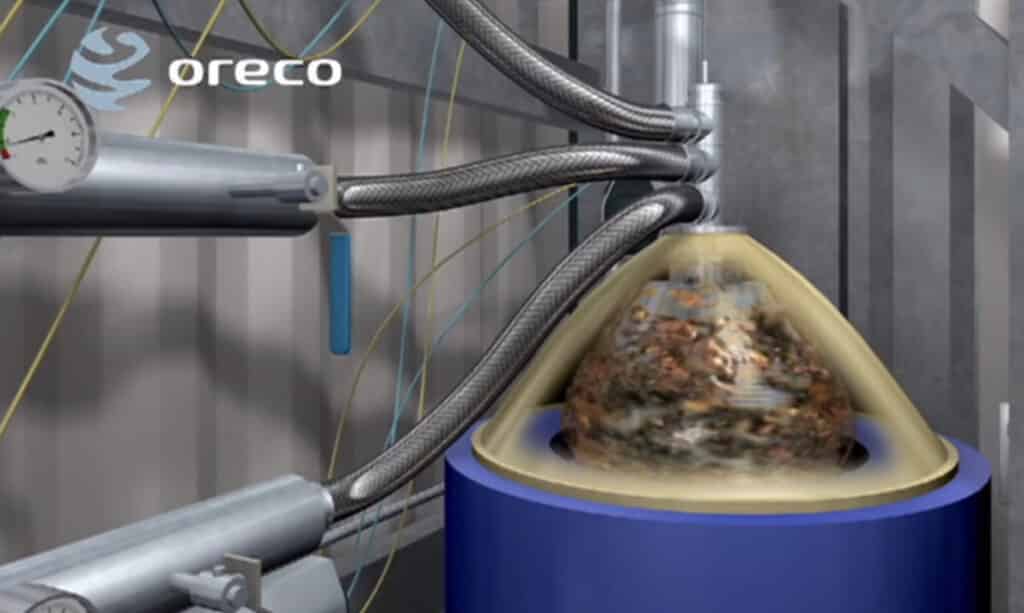
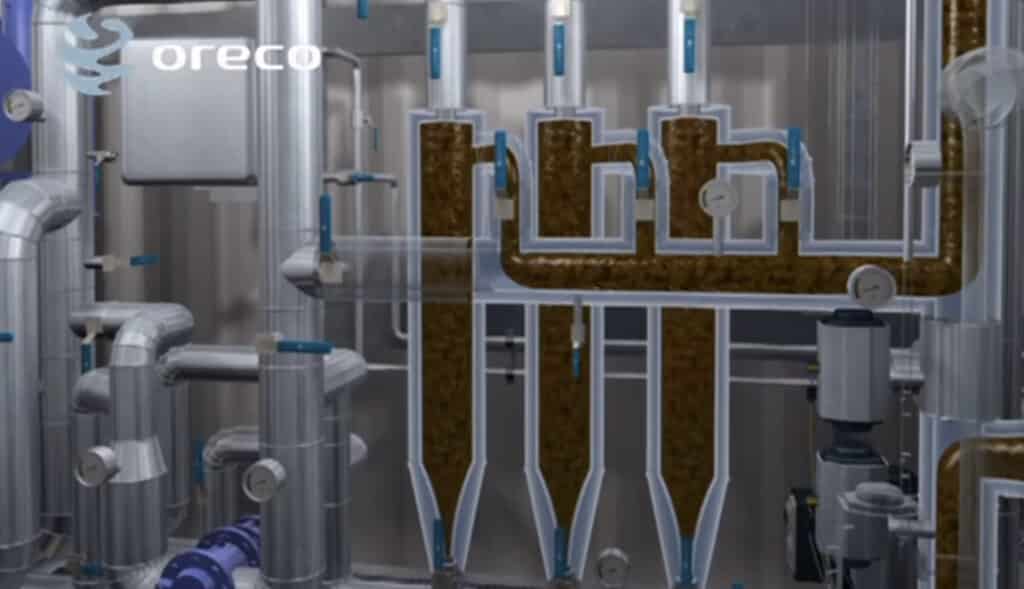
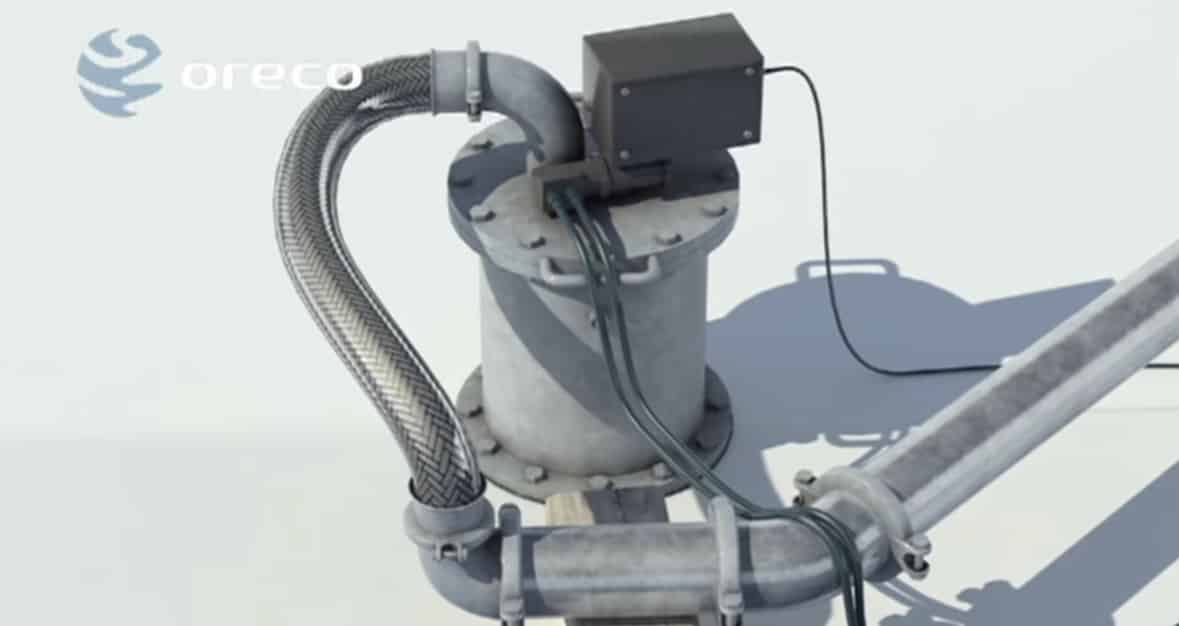
ORECO® specially designed and patented nozzle of the type “single nozzle sweepers” (“SNS”), uses the re-liquefied and recirculating oil as primary cleaning media. Their far-reaching high-impact jets make them extremely efficient.
BLABO® mixes, heats and shears the sludge, thus reforming it into re-liquefied oil.
The oil is pumped onto the recirculation module. If the viscosity is too high the oil is heated into the plate heat exchanger.
From the heat exchanger the oil is led to the hydro cyclones to separate the heavy solid particles from the recirculating cleaning media.
A booster pump returns the cleaner fraction to the storage tank where is it used to re-liquefy more sludge. The recirculation loop is complete.
The separation process takes place simultaneously with de-sludging.
The separation module enables tank owners to achieve specific separation requirements.
One can opt to run a liquid-solid separation only using the decanter or to perform a further oil-water separation of the liquid via the high-speed separator.
If the oil need further treatment it is pumped to the separation module for separation into clean oil, solids and water.
With the BLABO® system more than 95% of the oil in the sludge can be recovered and reused. The clean oil is pumped to the pipeline.
To clean the tank completely, it is now time to perform a water wash and skimming module comes into action.
The oil is skimmed off the water surface and pumped back to the tank owner as recovered oil. This procedure is repeated until there is no oil left in the tank.
The procedure ends with demobilization and de-installation in which the equipment, piping, and cabling have been disconnected, demounted, cleaned, packed and loaded onto trucks.